Manufacturing of Bricks
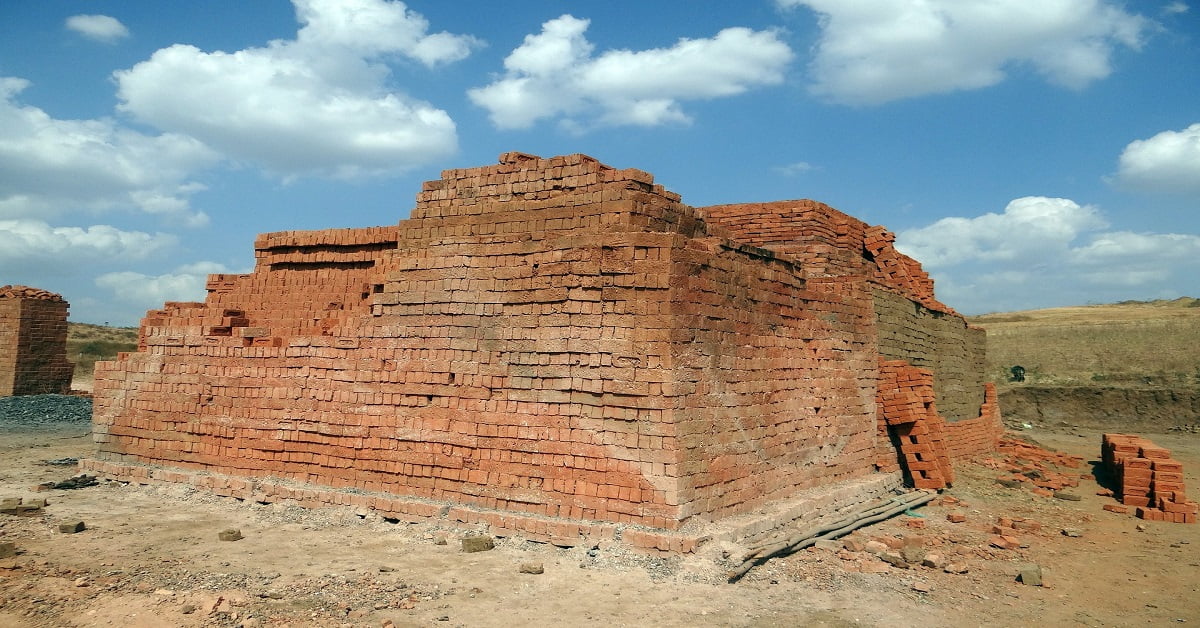
The process of manufacture of bricks consists of four stages.
Preparation of Clay
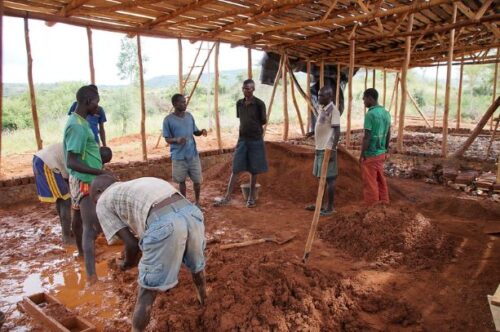
The clay used for manufacturing of bricks has to undergo the following steps:
Unsoiling of clay
The clay used for making brick must be free from gravel, coarse sand, kankar, lime and organic matter. The top layer of the earth contains impurities. Hence, remove 200 mm from the top earth. This is called as unsoiling of clay.
Digging
After unsoiling, dig the clay from the ground and spread out on plain surface. Remove the impurities like vegetable matter, stone, etc., from the spread out clay. Rollers are used for crushing if clay is present in lumps.
Weathering
Expose the cleaned clay to atmosphere for 3 to 4 weeks. The clay is heaped in plain ground. The height of the heap is about 60 – 120 cm. Turn the heap of clay upside down for at least twice. Maintain the clay as wet throughout the period.
Blending
Blending is the process of addition of ingredients to clay. Add sufficient amount of water to obtain right consistency. The additional ingredients that can be added are Fly ash, Sandy loam, rice husk ash, basalt stone. The addition of such ingredients in optimum range modifies shape of the brick, drying and firing behavior of clay. Also, the addition of those ingredients help to conserve agricultural land and use waste materials available in large quantities.
- Fly ash – Fly ash is a waste material from thermal plants. The chemical composition of fly ash is similar to brick earth. The addition of optimum quantity of fly ash helps to develop strength of clay on firing.
- Sandy Loam – The addition of sandy loam controls drying behavior of highly plastic clay.
- Rice Husk ash – The rice husk ash must contain unburnt carbon of about 3% to 5%. It must be free from extraneous matter. Rice husk ash is used with plastic brick red soil which shows excess shrinkage.
- Basalt stone dust – It helps in modifying shape, firing and drying behavior of clay.
Tempering
Tempering is the process of addition of water to clay and kneading of clay to make it stiff and plastic. Store the clay in cool place in layers of 30 cm for about 30 to 36 hours. For manufacturing good brick, pug mill is used for tempering. When pug mill is used, tempering of clay is called as pugging.
MOULDING
Moulding is the process of giving rectangular shape to the brick. The bricks can be either Hand Moulded (Example – fire brick), Machine Moulded (Example – all structural clay products) or Dry Pressed (Example – roofing, floor or wall tiles).
Hand Moulding
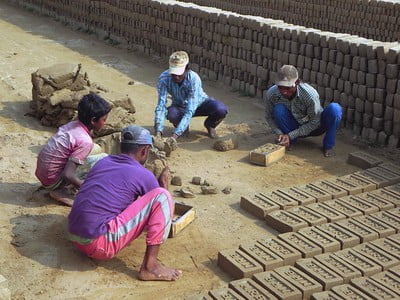
It is further classified into ground moulding and table moulding.
- Ground moulding – Ground moulded brick has no frog over it. Bottom surface of the brick is rough. Ground moulding is suitable when large and level land is available. A moulder can mould 750 bricks per day.
- Table moulding – Moulding of bricks is done on boards nailed to moulding table. The mould along with the clay is taken to drying site and is dried by removing the moulds. Table moulded bricks have frog. The size of the table is 2 m x 1 m.
Machine Moulding
Force the stiff clay into a rectangular opening of the size of a brick by using an auger. Cut the clay which is coming out of the opening by using a wire. Machine moulding of bricks is quick and economical.
Dry Pressed bricks
Feed the moist clay into mechanically operated press by means of applying high pressure. The clay in the mould takes the shape of bricks. Dry pressed bricks are more dense, smooth and uniform than ordinary bricks.
Drying of Bricks
Freshly moulded brick contains moisture of about 7% to 8%. Dry the bricks to remove moisture, control shrinkage and reduce fuel and time. Addition of sand reduces shrinkage and increases porosity. Drying of bricks reduces moisture content to 3% when exposed to atmosphere for about 3 to 4 days. Clay products are dried in open air or by using artificial drier. The temperature in artificial driers exceeds 120°C. Artificial driers are further classified into Hot Floor Drier and Tunnel Drier.
- Open Air Drier – Stack the bricks on raised ground. Protect the stack of bricks from bad weather and direct sunlight. A gap of 1 m is left between adjacent layers of stack. This ensures free movement of workers.
- Hot Floor Drier – Heat is applied by a furnace placed at one end of drier. It is used for fire bricks, clay pipes and terracotta.
- Tunnel Drier – The drier is heated by fuels using steam pipes. It is more economical.
Burning of Bricks
The burning of bricks is done in three stages as follows:
- Dehydration Stage – Also known as water smoking stage. The temperature of brick is about 400°C to 650°C. The pore water is lost. And so, the clay loses its plasticity.
- Oxidation Stage – The temperature is about 650°C to 900°C. The carbon present in clay is eliminated. Ferrous oxide is oxidized to ferric oxide. Oxidation must proceed at a rate which will allow these changes to occur before the heat becomes sufficient to soften the clay.
- Vitrification Stage – The temperature of brick is about 900°C to 1250°C. At this stage, the mass of brick is converted into glass like substance.
Burning of brick is done in clamps or kilns.
Clamps
A piece of ground is selected. The shape of the clamp generally trapezoidal in plan. The bricks and fuel are placed vertically in alternate layers. The amount of fuel is reduced successively in top layers. Each tier of brick has 4 to 5 layers of brick. Space is left between bricks for free circulation of hot gases around the bricks. After 30% loading of clamp, lower layer of fuel is fired and successively loading is done carefully. The top and sides of clamp are plastered with mud to prevent the escape of hot gases.
Number of bricks produced is about 2 to 3 lakhs and takes 6 months. The clamp yields 60% first class brick. Temporary structure. The floor of clamp is prepared in such a way that short end is slightly in the excavation and wider end is raised at an angle of about 15° from ground level. The thickness of this layer is about 700 mm to 800 mm. The total height of a clamp is about 3 m to 4 m.
Kilns
Kilns are permanent structure for burning of bricks. It maybe constructed underground (Bull Trench Kiln) or over ground (Hoffmann’s Kiln). The kilns may be rectangular, circular or oval. Kilns are classified into two types as:
- Continuous kiln – The bricks are burnt continuously in kiln. Example – Hoffmann’s Kiln and Bull Trench Kiln.
- Intermittent kiln – The bricks are not burnt continuously.
Great explanation!